Breve História da Metalúrgia (2ª Parte)
O enorme progresso alcançado hoje em dia a nível tecnológico deve-se em grande parte à evolução no domínio dos metais que se faz sentir desde os povos neolíticos.
A revolução científica do séc. XVII e a revolução industrial do séc. XVIII não se reflectiram de imediato sobre a tecnologia metalúrgica. No entanto, as primeiras observações com carácter científico das propriedades dos metais foram feitas por Jousse em 1627, e por volta de 1722, Réaumur tentou relacionar as propriedades do ferro fundido com a estrutura que observava com o auxílio dum microscópio.
Só a partir do séc. XVIII é que a metalurgia é descrita como uma ciência do estudo dos metais: ciência que estuda a estrutura, a composição, as características e as propriedades dos metais. Passa a ter como objectivo não só fabricar produtos metalúrgicos como também as suas causas e efeitos. Deste modo, à metalurgia extractiva já existente associou-se uma metalurgia física, ciência dos materiais.
A partir de 1855 com o ferro tão bem implantado nos materiais de construção, um novo metal, o alumínio, torna-se importante no desenvolvimento industrial da civilização. O alumínio, metal de baixa densidade, dúctil, estável e facilmente fundido não era fácil de produzir (envolvia muita energia). Preparava-se segundo a sequência bauxite® alumina® alumínio metalúrgico e foi nesta altura que se começou a aplicar electricidade à metalurgia.
Neste período (1855-1957) assistiu-se também à introdução nos processos metalúrgicos de sistemas de produção de aço. A capacidade dos altos fornos de conter ferro cresceu intensamente desde o primeiro alto forno.
O processo que Bessemer sugeriu foi fundir o "pig iron" (produto de alto forno, que é ferro no estado natural e normalmente contem 4.5 % de carbono e impurezas como fósforo, enxofre e silício) num forno reverbatório e descarbonizá-lo através do fluxo de ar pela sua superfície. Para evitar que as barras quentes de ferro expostas às deslocações de ar sofressem descarbonização Bessemer, introduziu o primeiro convertidor (reservatório aquecido que contem "pig iron" fundido) e, com este processo, fez reduzir suficientemente o preço do aço de modo a que este fosse usado em muito maiores quantidades.
Em 1875 a quantidade produzida de aço Bessemer em Inglaterra era superior a 700.000 toneladas; aço este que era usado por companhias de caminho de ferro, armamento e construção naval.
O convertidor Bessemer, juntamente com os fornos Siemens-Martin, e a produção de convertidores de aço e de fluxo de oxigénio constituíram as inovações que estiveram na base da metalurgia moderna.
A partir de 1863, usando uma técnica de polimento elaborada que envolvia abrasivos sucessivamente mais finos, Henry Clifton Sorby desenvolveu técnicas de observação microscópica e apercebeu-se que a textura da superfície de fractura dos aços depende dos tratamentos térmicos a que estes haviam sido submetidos e da sua composição química exacta. Após polimento e contrastação da superfície, Sorby observou pela primeira vez a microstrutura metalográfica do aço e descreveu a perlite. Os seus trabalhos estão na origem da metalurgia física que consiste no estudo das propriedades e composições dos metais. Estes estudos levaram ao desenvolvimento de ligas inovadoras mais apropriadas para aplicações particulares.
Neste século deu-se o desenvolvimento de uma série de novos elementos de análise, como os microscópios electrónicos de varrimento e de transmissão e o difractómetro de raios X, o que permitiu aos cientistas estudarem as estruturas existentes nos materiais e correlacionarem-nas com as propriedades observadas. Deste modo, os novos materiais que permitiram a construção de novos equipamentos levaram à descoberta de novas características e consequentemente de novos materiais que podem ter aplicação nas mais diversas áreas.
Aumenta-se a resistência dos metais com a adição de elementos de liga adequados (níquel, cobre, molibdénio, vanádio, tungsténio...). Os metais que mais recentemente começaram a ser usados são o zircónio, titânio, magnésio, níquel, cobalto, urânio entre muitos outros.
A evolução científica e tecnológica trouxe consigo os reactores nucleares originando deste modo problemas metalúrgicos nos componentes dos reactores tal como a resistência à corrosão, carácter de absorção de neutrões específicos, resistência à radiação, estabilidade mecânica às temperaturas de trabalho. O Zircónio é um dos metais mais usados com vista às dimensões destes problemas.
A transmutação de metais passou a ser uma realidade com a descoberta da radioactividade: Rutherford, em 1919, iniciou a transmutação artificial bombardeando nitrogénio gasoso com partículas alfa produzindo novos materiais - hidrogénio e um isótopo de oxigénio.
As ligas de titânio têm vindo a ser cada vez mais produzidas: em 1948 apenas 2 toneladas foram produzidas, em 1956 já foram 14000 toneladas; e o seu preço tem vindo a diminuir, continuando a ser, no entanto, relativamente elevado.
Gálio e índio são usados directamente em aplicações termométricas e em fusíveis devido ao seu baixo ponto de fusão, tério e germânio são semicondutores.
Nos últimos 80 anos tem-se apostado na produção de ligas e superligas metálicas, cujo resultado é uma melhoria nas propriedades. Isto deve-se às aplicações cada vez mais exigentes que nos rodeiam. Por exemplo, a indústria aeroespacial procura ligas com um peso mínimo sem alteração da sua resistência característica, como é o caso das superligas metálicas, que suportam, sem enfraquecimento das suas propriedades mecânicas, temperaturas até 1600ºC tornando simples os voos supersónicos e as missões espaciais; a indústria química, por sua vez, necessita de ligas para aplicação em equipamentos de extrusão de plásticos, aplicações criogénicas, turbinas, etc...
Muitas destas ligas são produzidas por Pulverometalurgia que consiste na introdução de um pó metálico num molde que é sujeito a elevadas pressões e temperaturas. Esta técnica tem por vantagem evitar uma grande perda de material que geralmente está associada às operações tradicionais de conformação e maquinagem e tornar possível a produção de microestruturas altamente homogéneas (com solidificação homogénea) tal como o fabrico de componentes com elevadas especificações de controle. Além desta técnica desenvolveu-se também a solidificação Super Rápida, processo este que promove um rápido escoamento de calor para o exterior (velocidades de arrefecimento muito elevadas, da ordem dos 105 ºK/s). Esta técnica permite a criação de ligas muito mais resistentes que os metais convencionais e com muito menor resistência à electricidade.
Como consequência da produção destas ligas por Pulverometalurgia e solidificação Super Rápida as temperaturas de trabalho das turbinas nas aplicações de aeronáutica têm vindo a aumentar 7ºC/ano. Note-se que (1) um aumento de 80ºC origina uma subida de 20% na propulsão do motor e uma significativa redução na economia de combustível.
Por outro lado a indústria mecânica (nomeadamente a General Motors) desenvolveu um carro movido a energia solar denominado "Sun Raycer" cujo motor, mais leve, pequeno e resistente que outros motores eléctricos é também produzido por solidificação Super Rápida.
Note-se também que a introdução de certas ligas metálicas amorfas nos núcleos dos transformadores que têm uma responsabilidade significativa nas perdas de energia eléctrica no seu transporte, permite reduzir as perdas de energia na ordem dos 100 biliões de KW/hora e que a sua aplicação nas células solares pode permitir a redução de custos de produção de energia de 4 dólares para 0,1 dólares/kWh(2). Desta maneira a energia solar poderá ser tornada viável.
O surgimento de novas ligas como as ligas com memória de forma têm várias aplicações em robots, válvulas, molas... Estes metais após serem dobrados e retorcidos regressam à sua forma inicial quando aquecidos ou arrefecidos a uma temperatura determinada.
No entanto a consequência do desenvolvimento da ciência e engenharia metalúrgica não é apenas a implementação de novos metais, mas também a introdução de novas técnicas de superfície (tratamentos superficiais por laser, nitroração iónica, CVD, PVD...) que alteram as suas propriedades, como é o caso da resistência ao desgaste, à corrosão e à oxidação mas não alteram significativamente o seu custo de fabrico.
A evolução cientifico-metalúrgica dos dias de hoje faz-nos deparar com metais cujas propriedades não se encaixam na classificação tradicional (dúcteis, bons condutores e relativamente pesados), como é o caso das ligas metálicas leves, dos metais orgânicos ou dos compósitos.
Muitos destes metais influenciaram tanto o modo de vida das populações que se tornaram indispensáveis ao funcionamento das sociedades modernas.
Há, porém, que ter em conta a selecção racional dos materiais e o modo de processamento tecnológico que deverá ser económico quer em custos, quer em tempo, não esquecendo o aspecto ambiental que envolve todo um processo de reciclagem ou de incineração tanto dos resíduos industriais, como dos produtos já usados. Pois é destas precauções, em grande parte, que depende o nosso futuro... e o futuro da história da metalurgia.
Tecnologia e Metalurgia
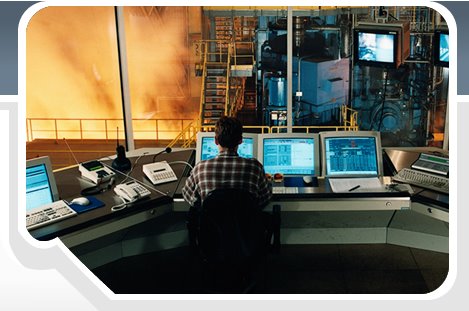
Assinar:
Postar comentários (Atom)
Nenhum comentário:
Postar um comentário